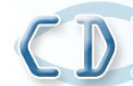


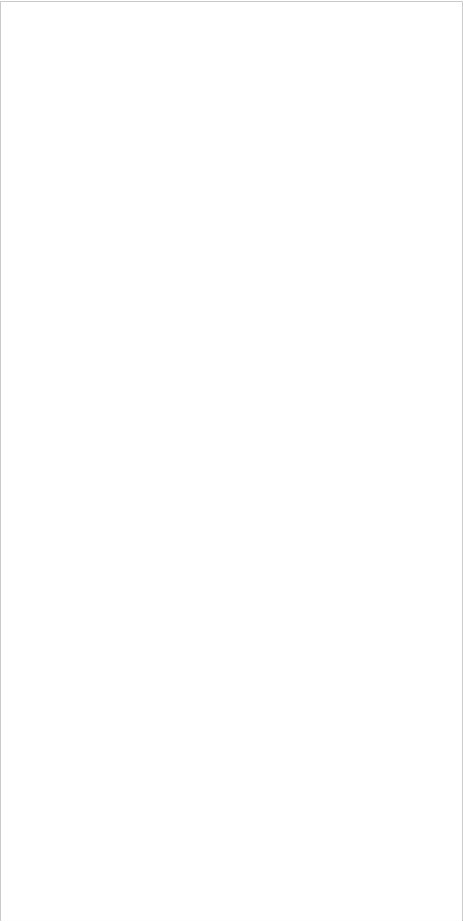
805-797-3748

Call Now!
Creative Data Devices, INC.
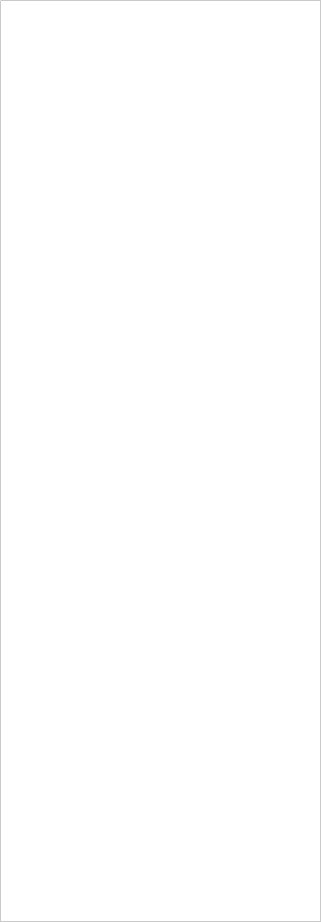
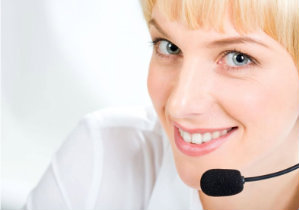
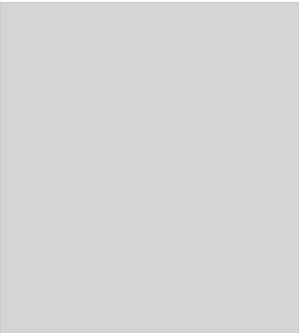
Will put a free quote form here

Speak with Mr. EMI Now!
Don't Be Fooled by Bad Literature
Call 805-797-3748
*or Complete this Simple Form*
We will never spam you or sell your email address.
Common Mistakes Causing EMI/EMC/ESD etc. Problems
Most of the task of controlling emissions and eliminating susceptibility issues is learning to control antennae and emission sources. We must see every trace or slot as an antenna and every active component as an emission source.
The most common failures occur because of poor power distribution or poor power decoupling. Design engineers work hard on the difficult signals and those signals are successful in the product. But the mundane power distribution gets neglected or designed with erroneous concepts that do not follow good RF practices. Often, we find emissions at individual frequencies in improperly bypassed products that can be reduced by as much as 40dB by just correcting that bypassing.
Chassis and signal grounds need to come together to form a single reference (there really is no such thing as a real ground) and splits in the ground and power planes are antennae. Some designs don't require planes, but for those that do it is important that they be done well.
Power must be adequately filtered with both bulk and higher frequency capacitors. This has to be done at every connector that passes power whether as input or output. Signal currents should not appear on those power cables.
Power planes should not extend all the way out to the edge of Ground/(Reference) planes. And no signal trace should be to the edge of a Ground plane.
Proper termination of clocks is important, but it is a distant second or third to proper handling of power and ground.
Connectors for external communication are important. AC coupled communications cables are particularly critical. The drive signal needs to be DC stabilized as close to the I/O connector as possible.
Shielding is often required but that does not correct an otherwise poorly designed system. Generally there is no such thing as a perfect Faraday Cage. If, however, the product is well designed and still there are undesirable emissions or susceptibility issues, a well designed enclosure can take care of the problem. Design for overlapping, foldover corner connections of all pieces of the enclosure. The connections must be done using large surface area connections.
Normally shielded cables should be connected at both ends. The exceptions are for long cables that connect between devices of radically different power source. The shield must be continuous all the way to the connector shell. For Aluminum foil shields the termination should be done with a crimp ferrule with a solder connection (360 degrees) to the connector body.
• We offer consulting services for clients
worldwide.
• Our consulting service starts from
wherever your project is.
• We hold to high standards of
engineering excellence and integrity.
